
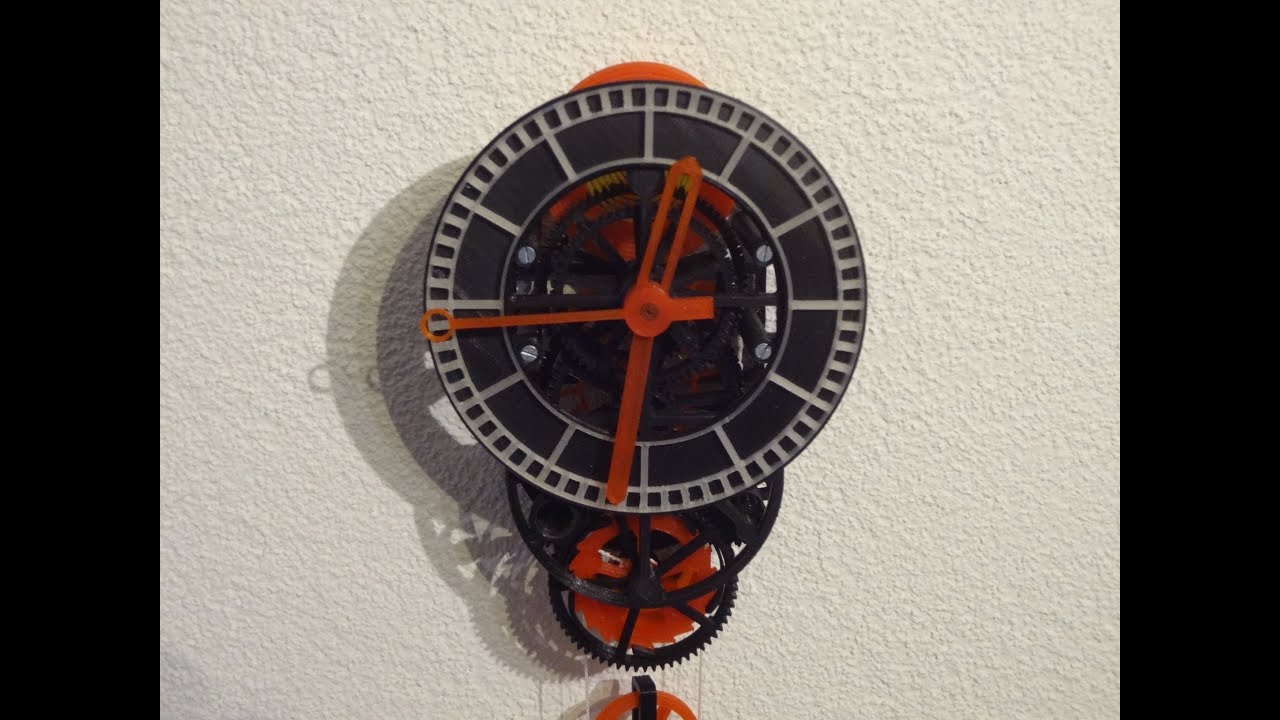
“I ask them to think completely off the rails, into new stuff that’s never been printed before,” Hart says. The students attend lectures, learn to use commercial 3-D printers to fabricate custom objects, and square off in a bridge-building competition, to see who can design and print the sturdiest bridge with the lightest weight.

In 2013, Hart created an MIT graduate course, 2.S998 (Additive Manufacturing), that explores the fundamentals, applications, and implications of 3-D printing. John Hart, the Mitsui Career Development Associate Professor in Contemporary Technology and Mechanical Engineering at MIT, says early education on 3-D printing is the key to helping the technology expand as an industry. In recent years, access to more affordable desktop 3-D printers has helped fuel the maker movement, giving students and hobbyists a chance to experiment with the technology.

The technology has been used to make hip and dental implants, as well as architectural models and aerospace tools, including a socket wrench that astronauts recently printed aboard the International Space Station.įor the most part, however, 3-D printing is a small-scale fabrication tool, used by engineers and designers to quickly print up a prototype. Three-dimensional printing - and additive manufacturing in general - is the process of depositing material, layer by layer, in patterns determined by computer software, to precisely fabricate a three-dimensional object. It’s been more than 30 years since the invention of 3-D printing, and yet in some ways the technology is still a frontier of unexplored potential.
#FINAL PRINT MECHANICALS PLUS#
Facebook Twitter LinkedIn Google Plus Email
